Understand the settings in the Inventory Details tab
- General Information
- Inventory Type
- Normal – used as a regular item for sale or purchase
- on-Physical – an item where quantity tracking is not required (ie: Labour)
- Manufactured – top-assembly item for a Production Order Template – this item needs to be ‘built’ to be sold (see also Manufactured Inventory (Bill of Material) this chapter and Production Manager)
- Kitted – compilation of one or more Normal, Non-Physical and/or Manufactured items, or a combination of these – this item can be assembled on-the-fly in a sales order (see also Kitted Inventory)
- Raw Material – used in a Manufactured Inventory Item through Production Orders (no difference in functionality from a ‘Normal’ item)
- Macro will group together items commonly sold together but priced independently (see also Macro Inventory)
- Serial / Lot Numbering – track the activity of any item or Bill of Material component or Kit Component using Serial or Lot numbers
- Activate – Edit > Company Settings > Inventory - Use serialized Inventory
- Inventory Type
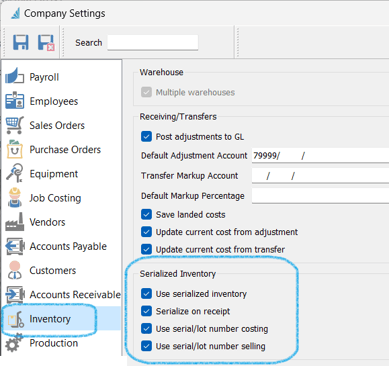
-
-
-
Use serialized inventory
Serialize on receipt
- checked - the serial number is Vendor-assigned, and entered at time of inventory receipt
- unchecked - assigned by your company and entered at the time of sale
- once the Inventory Item is saved as a
Serialized Item, a Serial Numbers tab will appear where Serial Number activity will be tracked and viewed (see Serial Numbers / Lot Numbers tab)
-
-
-
-
-
-
Serial / Lot Number Costing / Selling - during receipt of a serialized item, the system will track the cost / selling price of that specific receipt / build transaction
-
-
-
-
-
- Lot Numbered – once selected, the option will appear to choose consumption method at the time of the sale of this item
- Lot Numbered – once selected, the option will appear to choose consumption method at the time of the sale of this item
-
-
-
-
- Consume by Choice – the user can manually choose the lot
- Consume by Date Received – system will automatically use oldest lot number
- Consume by Alphanumeric Order – system will automatically use lowest lot number, either alpha or numeric or alphanumeric
- Consume by Expiry Date – system will automatically use the lot with the oldest expiry date
-
-
-
-
-
- Note: lot expiry dates are established at the time the goods are received, with an option to establish the Default Expiry Days in Inventory Details tab and to enforce an Expiry Date in the Inventory setup - Expiry Date Required:
-
-
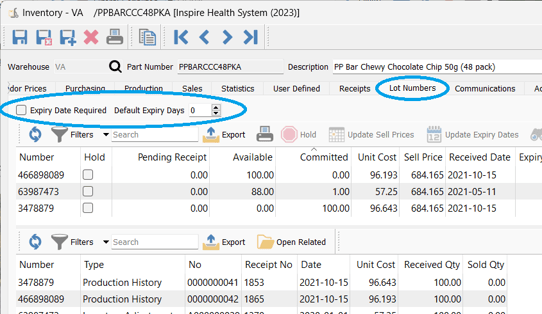
-
-
-
- once the Inventory Item is saved as a Lot Numbered Item, a Lot Numbers tab will appear, where Lot activity will be tracked and viewed (see Serial Numbers / Lot Numbers tab)
- Lot Number Costing - during receipt of a serialized / lot numbered item, the system will track the cost / selling price of that specific receipt / build transaction
- setup in Edit > Company Settings > Sales Orders / Orders tab > Inventory > Use serial / lot number costing and Use serial / lot number selling
-
- Product Code - see Inventory - Product Code
- Alternate - enter your Part No that can substitute for this Inventory item
- if stock is insufficient on a Sales Order, you will be prompted to use this Alternate Part No (if it has available stock):
-
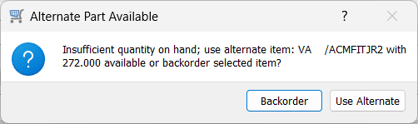
- GL Accounts
- Sales Department – establishes which GL Accounts are affected by the sale of this item (overrides Sales Department established at the Product Code level)
-
-
- Access - through the
Browse button
- Access - through the
-
-or- Inventory > Sales Departments
-
-
- click
New
- enter a Code of your choice
- enter a Description of your choice
- establish the Inventory Account / Cost of Sales Account / Revenue Account
- click
-
- note that if a Sales Account and / or Cost of Sales and / or Inventory GL account is not present for any Sales Department, those allocations will default to the accounts established in Special Accounts (Company Settings > General Ledger > Special Accounts)
- User Defined are not system-integrated but can be used for Filters / Searches / Reports and can be re-named in Company Settings > Variables:
-
- Misc
- User Type
- Physical (Attributes)
- Pack size – for reference only, to determine how many items are in the default unit of measure
-
- Weight –loads in Sales Order - set Unit in Edit > Company Settings > Inventory - Weight Units
- Location – for reference only, to determine where the item is located in the warehouse
- Country of Origin – option to establish the Country of Origin
- HS Code - The Harmonized System Database Code is structured upon a six-digit nomenclature, used as a basis for their Customs tariffs
- visit http://www.wcoomd.org/ or http://www.cbsa-asfc.gc.ca/publications/pub/bsf5118-eng.html for more information on HS Codes
- Weight –loads in Sales Order - set Unit in Edit > Company Settings > Inventory - Weight Units
Pricing and Costing
-
- option to establish the Decimal Precision for Sell and Cost values in Edit > Company Settings > Company > Numbers:
- Price per PK (ie) represents price for the stock unit of measure
- Average cost / Margin % – averages the costs of items purchased that are currently in stock
- Current cost / Margin % – updates with cost from each new purchase order that this item is received on
- Standard cost / Margin % – not system-integrated, but can be used to insert a cost manually (User Settings permitting) - Cost Method for sales is established in Edit > Company Settings > Inventory > Cost Method - Average is always recommended
- option to establish the Decimal Precision for Sell and Cost values in Edit > Company Settings > Company > Numbers:
- Purchasing
-
- Primary Vendor – establish the preferred vendor for auto-creation of purchase orders (see Purchase Orders - Requisitions )
- PO No – displays the most recent purchase order still open in the system for this item
- Due date – displays the ‘Required date’ from the most recent purchase order still open in the system
- Reorder Point – is used in conjunction with customer order / backorder quantities and Minimum Buy Quantity (Min. Order Qty) to calculate the Suggested Order Quantity in the Inventory List which is used in conjunction with Requisitions
- Order Qty can be established if your Vendor required - is used in conjunction with customer order / backorder quantities and Minimum Buy Quantity (Min. Order Qty) to calculate the Suggested Order Quantity in the Inventory List
- Duty % - option to establish a default percentage for pro-rating duty charges on purchase order receipts for landed cost which also gets updated from a Purchase Order (see Purchase Order - Receive - Landed Costs)
- Freight % - option to establish a default percentage for pro-rating freight charges on purchase order receipts for landed costs, which also gets updated from a Purchase Order (see Purchase Order - Receive - Landed Costs)
- Extended Description – to add description for this item, for use in filters, searches, reports and forms, typically used for web store integration